Concrete is one of the most versatile building materials in the world. It is a mixture of cement, aggregates (like sand and gravel), and water that hardens over time to create a strong material.
Concrete can be molded into any shape. It is usually reinforced with steel to increase tensile strength and durability. Contact Commercial Concrete Contractors Dallas TX now!
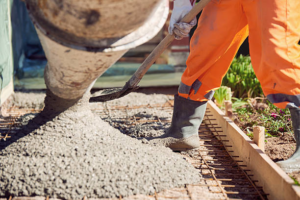
Concrete’s exceptional strength, durability and versatility make it the material of choice for constructing structures such as highways, bridges, dams and skyscrapers. Reinforced concrete, which incorporates steel bars or meshes within the mixture, enhances its tensile strength and resistance to bending and cracking.
The properties of concrete are influenced by the mix proportion of cement, sand, aggregates and water. The ratio of these components, which is referred to as the concrete grade, controls the various concrete properties such as compressive strength and flexural strength.
When water is added to the concrete mix, a chemical reaction known as hydration takes place, with the chemicals in the cement reacting with those in the water and forming new compounds and crystals which interlock with the aggregates. This process is what gives concrete its strength, and it continues to take place as long as water is present in the concrete.
Once a concrete mixture has been mixed it can be transported and placed in the structure where it will be used. Depending on the distances involved, the quantity needed and other details of application, it may be hauled in trucks, poured free of gravity or through a tremie, or pumped from a pipe.
If the concrete is poured in layers, it must be allowed to set between each pour. This is achieved by allowing the concrete to cure for a period of time, with curing conditions set according to the project specifications.
Once the concrete has been poured and allowed to cure, the next step is reinforcement. The addition of steel reinforcement, either bars or meshes, significantly enhances the tensile strength of concrete and allows it to be used in applications that require significant bending or flexing.
The elasticity of concrete is determined by the Poisson’s Ratio, which is a measure of the lateral strain, or twisting strain, to the axial stress in the concrete when it is stretched or compressed. This ratio is a key factor in the design of concrete structures, and it can be modified by changing the mix composition or by the use of different forms of reinforcement.
Durability
Concrete structures are used in many different ways, and they need to withstand a variety of environmental stresses. Insufficient durability can cause damage and deterioration, which leads to expensive maintenance and repairs. A lack of durability can also increase embodied energy and waste, which is why it is important to consider the durability of concrete during design and construction. High durability concrete structures can reduce the amount of resources and carbon emissions that are incurred during their lifetime, making them a more sustainable choice for both developers and building owners.
The durability of concrete depends on several factors, including the water-cement ratio, admixtures, curing practices, environmental conditions, and maintenance and repair strategies. Engineers can help to ensure that concrete is durable by specifying performance-based requirements for the mix design, utilizing supplementary cementitious materials (such as fly ash, slag cement, and silica fume), ensuring that the construction site has adequate curing facilities, and monitoring the structure for signs of distress throughout its lifespan.
One of the most important aspects of a concrete’s durability is its ability to resist chemical migration. Aggressive chemicals, such as chlorides, salts, and sea water can penetrate concrete, causing deterioration. Concrete can be made more resistant to these chemicals by using specialized admixtures, such as corrosion inhibitors, and by providing adequate curing practices.
In addition to its physical durability, concrete must be able to withstand changes in volume due to temperature fluctuations. Concrete typically shrinks during the drying process, which can lead to cracking. Fortunately, this phenomenon can be minimized by using a low-water-cement mixture and adding workability enhancing admixtures. These admixtures reduce the tendency of cement particles to bind together in sludge-like flocs, which escape hydration and weaken the concrete.
The Silver Bridge disaster is a tragic reminder of the importance of considering concrete’s durability during construction. Efforts to improve the durability of concrete have resulted in innovative solutions that offer substantial benefits for the construction industry, such as reducing maintenance costs and minimizing embodied energy. Concrete’s inherent alkalinity also helps to protect steel reinforcement from corrosion, extending the service life of reinforced concrete structures.
Chemical Composition
Concrete is a construction material composed of cement, fine sand and coarse aggregate, all mixed with water. Six billion cubic meters of the material is produced annually. Occasionally other materials are added to the mix, called admixtures, for special purposes or to suit certain building conditions. They can alter the fluidity of concrete and increase (accelerate) or decrease (retard) the rate at which it sets.
Cement is made from oxides of calcium, silicon and aluminum. The chemical formula for portland cement is CaO + SiO2 + AlO CaSO4 – Ca(SO4)2. Cement binds the aggregate to form concrete by a process called hydration. This is a controlled chemical reaction. The main products of hydration are a calcium silicate hydrate and a magnesium silicate hydrate. They give the concrete its strength.
The composition of cement also determines its permeability. It should be low. This can be achieved by adding a low amount of air-entraining admixture to the mix or using sulphate-resistant cement, especially for structures exposed to aggressive environments.
Another factor is the physical properties of the aggregates, which affect how easy it is to work with. Larger, rough-textured aggregates tend to separate from the concrete. This is known as segregation and increases with a lean mix or high water to cement ratio.
Using fly ash as an additive can help reduce the cement content and lower the water to cement ratio. It acts as a substitute for some of the Portland cement, and it can contribute to the development of strong concrete by reacting with a chemical by-product of the hydration reaction, calcium hydroxide. This helps to remove the by-product from the concrete and prevents it from causing deleterious effects such as increased porosity and efflorescence – the formation of calcium carbonate crystals on the surface of the concrete or mortar.
Other admixtures include plasticizers and superplasticizers, which can increase the flowability of concrete without altering the water to cement ratio. They can also increase the slump of a concrete mix by changing the viscosity of the water. These are important to ensure the concrete can be placed where it needs to go and to make sure that it is well compacted.
Water Resistance
Concrete is the second most popular construction material in the world and is used for a variety of purposes. It is a durable material that is highly resistant to erosion. While it may deteriorate over time, this is typically caused by chemicals and moisture permeating the structure, not by water itself. Waterproof concrete, however, is impervious to both moisture and chemicals. The process of making waterproof concrete involves adding a variety of different additives to the mix, but primarily consists of enhancing the concrete’s internal structure and impermeability.
Typical concrete is a porous material that relies on its network of capillaries to move water through the structure. This can lead to a number of issues, such as cracking that allows water in and out, which in turn weakens the structure. In order to make concrete more resilient, waterproof additives can be added to the mix to help it resist the penetration of moisture and chemicals.
A common way to improve the water resistance of concrete is by incorporating air bubbles. These bubbles allow water near the surface to escape during freeze-thaw cycles, preventing spalling of the concrete. This method is especially important for structures that are exposed to harsh climates, such as tunnels.
In addition to using air bubbles, it is also important to ensure that the aggregate in concrete is of a high quality. The fine aggregate should be clean, hard and well-graded, which will reduce the amount of cement paste needed to hold together the coarser material. This will increase the strength of the concrete and its overall durability.
Another common way to enhance the water resistance of concrete is by adding a type of chemical-resistant polymer, such as graphene. These additives are mixed into the concrete during production, and can bind with the minerals in the aggregate to create a waterproof barrier that is extremely strong and durable.
In a study comparing SEM-1, SEM-2 and SEM-4 concrete, X-ray diffraction patterns reveal that the addition of fly ash and CCCW significantly improved the microstructural characteristics of the concrete. This was attributed to the fact that they enhanced the interconnectivity of the concrete’s internal matrix, increasing its structural compactness. The addition of CCCW also reduced the gaps in the transition zone between the fibers and the concrete’s matrix, which is crucial for allowing the fibers to fully exert their crack-resistant effects.